Fabricación
Materias primas
El vidrio es un producto inorgánico que se ha enfriado hasta alcanzar un estado rígido sin experimentar cristalización. Los principales componentes que intervienen en el proceso de fabricación de los envases de vidrio provienen de la naturaleza, existen en grandes proporciones y son de fácil extracción, asegurando un mínimo impacto ecológico.
Además, los procesos tecnológicos aplicados en el proceso de fabricación de los envases de vidrio han hecho que se produzca una disminución constante en la extracción de materias primas, a lo que se suma la utilización del casco de vidrio (vidrio reciclado) para la fabricación de envases. El hecho de que el envase de vidrio se pueda reciclar al 100% sin pérdida de calidad ni cantidad, (reciclado integral) contribuye a la protección del medio ambiente.
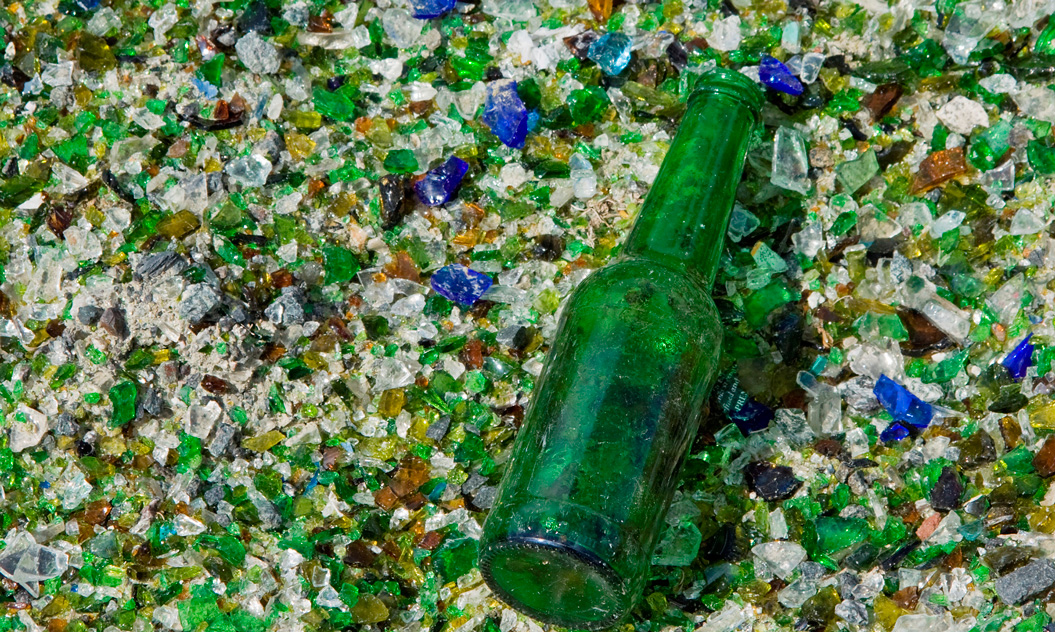
De forma general, las principales materias primas que se utilizan para la fabricación de envases de vidrio son, además del mencionado casco de vidrio, arena de sílice, carbonato de sodio y caliza, y se pueden clasificar en los siguientes grupos:
- 1. Vitrificantes
- 2. Fundentes
- 3. Estabilizantes
- 4. Componentes secundarios
Estas sustancias son el principal componente y son responsables de la creación de la red vítrea.
Componentes que favorecen la formación del vidrio, rebajando su temperatura de fusión y facilitando su elaboración.
Elementos que ayudan a reducir la tendencia a la desvitrificación.
En este apartado estarían encuadrados los afinantes, colorantes, decolorantes, opacificantes, etc.
Proceso
El proceso de fabricación de los envases de vidrio comienza cuando las materias primas son mezcladas y conducidas automáticamente al horno de fusión, a temperaturas próximas a los 1.000º centígrados.
Estos hornos funcionan 24 horas al día y 365 días al año durante 12 o 15 años (la vida útil de un horno). En ellos, las materias primas, incluidos los envases de vidrio procedentes del reciclado, entran por un extremo (enforne) y salen por el otro, una vez fundidos y acondicionados, a través de varios brazos (feeders) o canales de calentamiento/enfriamiento, dependiendo del tipo de envases a fabricar. A una temperatura próxima a los 1.000º centígrados, el vidrio fundido es cortado en gotas de un peso igual al del envase y distribuido a los diferentes moldes que posee la máquina de fabricación, donde mediante una serie de procesos de presión, prensado y vacío, se da forma a los nuevos envases. De forma general, las partes principales de un envase de vidrio son boca, cuello, hombro, cuerpo, talón, fondo y picadura (superficie cóncava en el interior del fondo). En función de la utilidad que se vaya a dar a los envases, se pueden distinguir dos grandes familias:
![]() |
![]() |
Botellas, destinadas generalmente a contener productos líquidos. | Tarros, diseñados para alimentos sólidos y semisólidos. |
Existen dos técnicas para la fabricación de envases: el soplado-soplado, utilizado habitualmente para la fabricación de botellas, y el prensado-soplado, desarrollado inicialmente para los envases de boca ancha (tarros), aunque actualmente también se utiliza para los envases de boca estrecha o botellas. Las máquinas utilizadas habitualmente son longitudinales de tipo IS constituidas por varias secciones que funcionan de forma independiente y que pueden pararse (ya sea una o varias) mientras las demás siguen produciendo.
Normalmente constan de 6, 8, 10, 12, 16 o 20 secciones y cada una de ellas puede trabajar en S.G. (simple gota o un envase por sección), D.G. (doble gota o dos envases por sección), T.G. (triple gota o tres envases por sección) e incluso C.G. (cuádruple gota o cuatro envases por sección).
Una vez fabricada la botella o tarro de vidrio, y aún a una temperatura elevada, es introducido en un túnel (archa) de recocido para evitar la formación de tensiones internas -debidas a un enfriamiento rápido- mediante temperaturas controladas. Los envases pasan por este túnel lentamente, recalentándose, y posteriormente son enfriados de una manera predeterminada. Así, el vidrio adquiere un mayor grado de resistencia.
Control de calidad
A la salida del archa de recocido, los envases son tratados en su cara externa para disminuir el coeficiente de rozamiento entre ellos y permitir un fácil deslizamiento por las líneas de inspección y embalado automático. Al final, un alineador distribuye los envases a las diferentes líneas de inspección y transporte. Una serie de máquinas electrónicas controla el 100 % de los envases y elimina aquellos que no cumplen las exigencias de calidad previstas.
Habitualmente son máquinas optoelectrónicas que se encargan de realizar controles dimensionales y funcionales del envase. Todas estas máquinas están vinculadas a un ordenador, donde se almacena y trata toda la información. Dado el elevado número de envases que se producen anualmente, estas máquinas realizan un proceso de control que sería imposible realizar hoy al 100 % por personas. Mientras, el control humano es llevado a cabo por personal altamente especializado. Este control y la eficacia de las máquinas son los que determinan si los envases producidos son aceptados o rechazados.
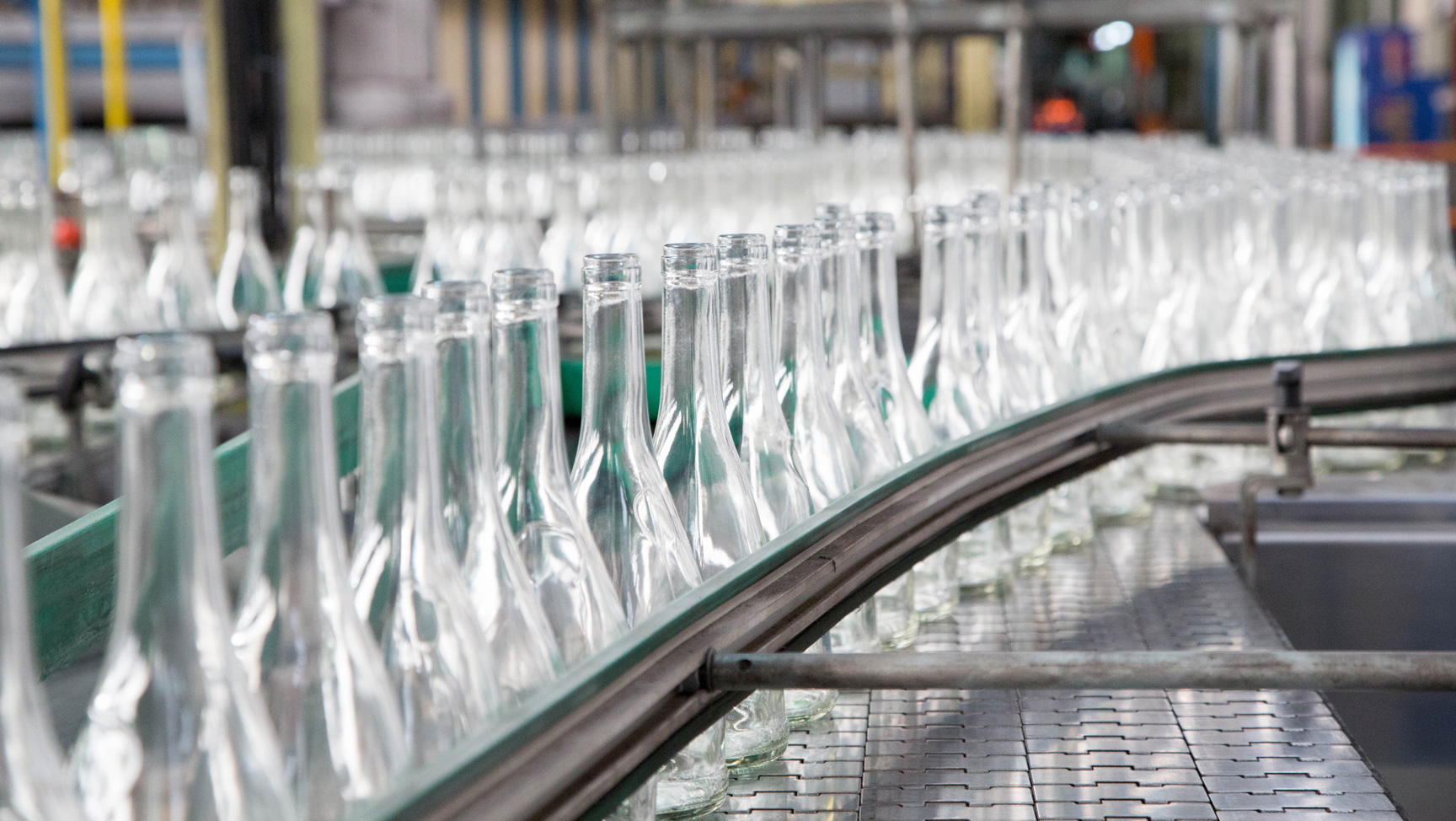
Embalaje
Por último, tras las máquinas de inspección se encuentran los paletizadores, encargados de embalar la producción. Una vez paletizada, esta es recubierta con una funda de plástico retráctil y pasada a través de un túnel de retracción o marco que contrae la funda sobre los envases y los protege de una posible entrada de polvo u otro elemento durante su almacenamiento y transporte.
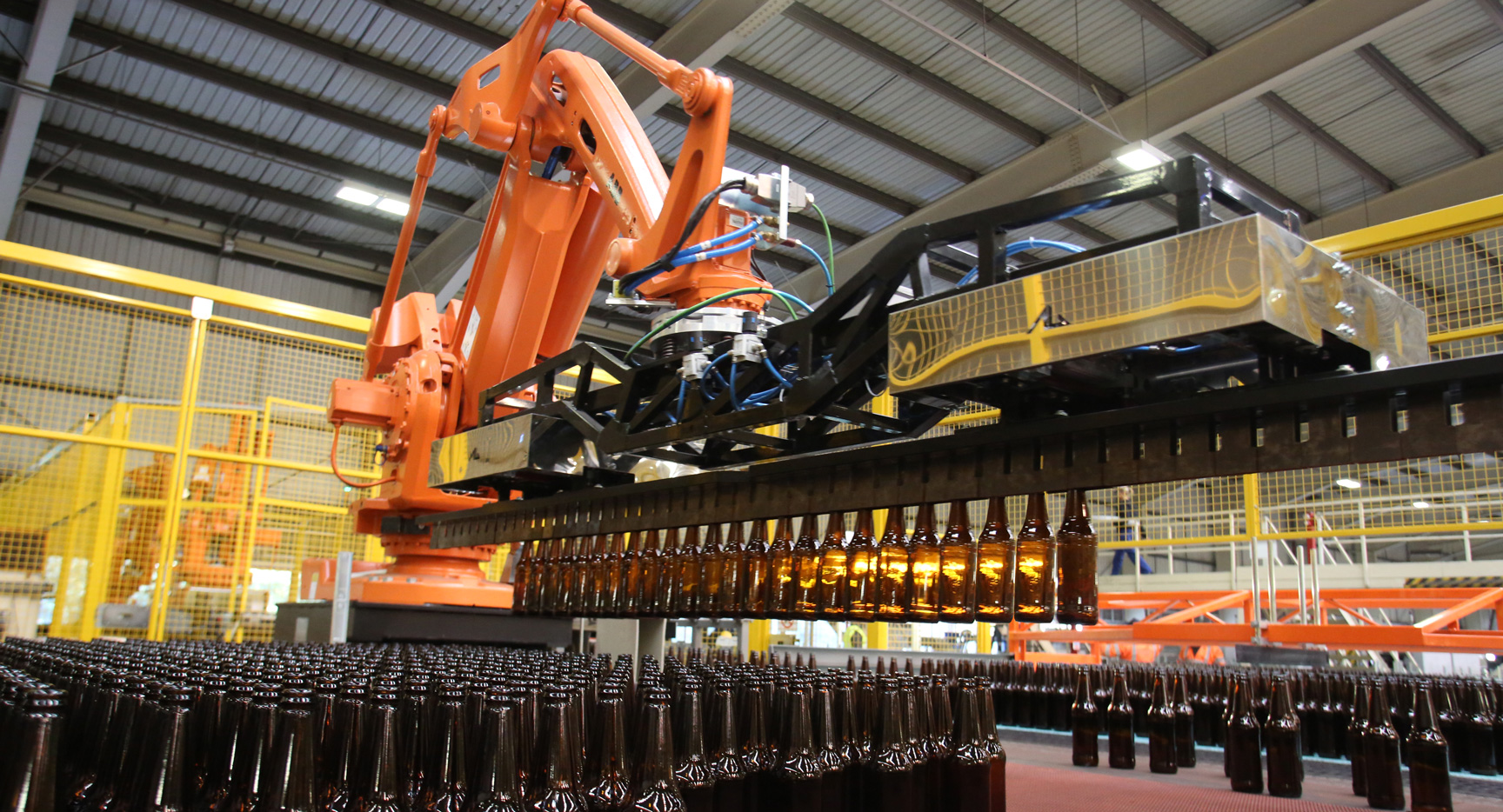